Power is required for egg production, packaging and shipping.
In the 1920s most eggs came from small flocks kept in fenced yards. In the 1930s, hens were moved indoors to protect them from weather, predators and disease. Each hen laid about 150 eggs per year.
In the 1960s, cage systems became predominant with farmers. Conveyor belts were introduced to move eggs from station to station. Farmers and scientists began working together to make sure hens were healthier and more productive.
Concentrated efforts began to reduce the risk of Salmonella and enhance hen well-being as a priority in the 1980s. The 1990s marked the introduction to quality assurance programs.
Scientific Advisory Committee recommended guidelines for hen care in conventional cages in 2002. In 2006, Certified Cage-Free guidelines were introduced. Egg farms transition to cage-free methods to meet the organic demand.
Today, consumption of eggs is at an all-time high in the United States. Over 7 billion table eggs were produced in 2017
see the AEB report here. Egg farmers work to balance high standards with safety and affordability. Environmental responsibility and hen well-being is considered in designing new hen housing. Many consumers believe that a less stress and anorganic environment increases the quality and taste of the eggs.
Automated Egg Production & Processing Facilities
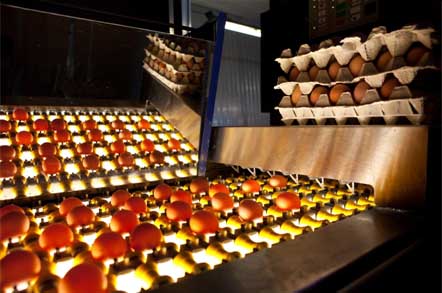
Automated farming begins at the hen house and ends with the final shipping of the product. An automated hen house can feature food, water, humidity control and egg collection. Food is distributed by conveyor or individual feeders. Water can be solenoid controlled or comprised of a open loop design.
Hens return to laying or nesting boxes to lay. It is not uncommon for well-maintained hens to lay more than one time per day. Eggs are routed from the laying box to the next stage via conveyor belt. If multiple hen houses are contained in the complex, eggs can be transported to a central processing plant.
Each egg is cleaned and moved to the quality inspection process. After the egg passes the inspection process, it is packaged and moved to a cold storage unit in preparation for shipping.
Automation is often determined by farm size. Large farms with multiple hen houses can have a network controlled at a home location. Individual hen houses and the process facility would have individual controls in the event of a communication failure.
Standby Diesel Generators and Commercial Egg Farms
Egg farms can be placed into the same category as any food production facility. Loss of power equal loss of production. Loss of production can be in products like eggs or hens, and can rapidly result in financial losses if hit by an unplanned outage.
A properly sized diesel generator can provide all emergency power needs. Generator Source has a long history of working with commercial egg farms of all shapes and sizes throughout the US and Canada. We can design or upgrade a system for any agricultrual environment that will insure dependable power when utility power is lost. Give us a call today to talk to one of our backup power representatives or
contact us online.