Cogeneration Technology Basics
All
generators for sale produce a certain degree of heat during electricity generation which can be utilized in a method called cogeneration. Cogeneration, or waste heat recovery, can be used to both heat and cool large buildings or use potential energy to power any number of industrial applications.
On average most engines lose about 50% of their thermal energy. With cogeneration, power plants can potentially reach up to 80% efficiency overall. This article will discuss the engineering aspects behind cogeneration and the practical applications currently in use throughout the world.
Cogeneration or CHP (combined heat and power) can be defined as procurement of two forms of energy from one fuel source. For example, a generator for sale produces electrical power as the primary energy source and waste heat as the secondary energy source. Often times the term “Cogeneration” is used incorrectly. Cogeneration does not refer to the operation of two generating sources working in parallel; such as two generators linked together as a one-unit source of power.
Another example would be a wind turbine generator in parallel with an engine genset. In these examples, the system is not obtaining electricity and heat simultaneously using steam from the same boiler. The energy captured from a true cogeneration system would normally be released into the natural environment.
Cogeneration is one of the leading technological advancements for achieving fuel efficiency. Under the right circumstances, power generation systems can achieve 50%-200% gains in efficiency or more over their current setup. Increasing concern about carbon dioxide emissions makes reduced use of fossil fuels urgent for the future. Instead of a complete change in power production technology (solar, wind, hydroelectric) companies are gaining efficiency much more cheaply through cogeneration.
The primary power source can be any form of prime mover driven power such as, but not limited to, electrical generation systems, blowers, desalinization units, pumps, air compressors or centrifugal (absorption) chillers. The thermodynamic heat recovered from the prime mover is usually in the form of steam or hot water. The prime mover process transforms into a
cogeneration system when the heat ejected from the prime mover, which is normally wasted, is recovered and is used in a heat consuming device. The primary difference between a gas turbine engine and a reciprocating engine is the way the heat is ejected.
It is important to note that cogeneration projects should only be considered if there is an ongoing need for using waste heat. It is not an economical solution if waste heat is only used for a few months out of the year. A cogeneration system that uses waste heat in the winter to heat a space would also need to use that waste heat during other seasons. For example, through 7 cogeneration plants, Con Edison distributes 66 billion kilograms of 350 °F steam each year to 100,000 buildings in Manhattan. The majority of these buildings are set up for both heat and air condition via steam. It would be a waste of money to use steam only to heat the building and then install individual separate air conditioners. Smaller cogeneration plants are perfect for hospitals, hotels, industrial plants, and university campuses.
If there is a disparity between electricity and heat use one or the other can be sold in a power purchase agreement. For example, if there happens to be a greater demand for heat than electrical power it can be sold directly to a utility company. Conversely, in some colder urban areas, excess heat production can be sold to a gas company for distribution to residential households.
Types of Cogeneration Plants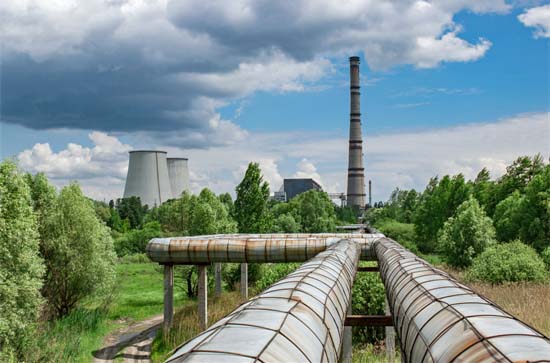
The most common type of waste heat recovery systems is steam and hot water. Most engines have a maximum jacket water outlet temperature of 210 °F. Other engines may be operated at temperatures of 260 °F. Engines must be specifically configured to operate at a higher temperature.
However, for most applications, 210 °F is hot enough to meet all needs. Low-pressure steam is capable of being generated from the jacket water at 250 °F - 260 °F. This temperature (with a properly configured engine) can be generated using a cooling application where steam forms in the engine jackets themselves and then rises due to the difference in density between the water and steam. Before considering a cogeneration plant it is best to speak with a professional electrical contractor to determine what jacket water configuration is needed.
Another method of producing low-pressure steam from the jacket water of the engine is through the pumped circulation of the water via the cooling system. Liquid water from the steam drum is pumped through the engines and the jacket water heat is transformed into steam as it enters the steam drum compartment.
15 PSIG to 250 PSIG of steam can also be generated with any gas turbine or diesel genset’s exhaust. Most exhaust systems are also designed with the optional fired steam boiler which is utilized by an exhaust gas bypass valve. Exhaust heat can be used in conjunction with the jacket water heat to create 15 PSIG steam or it can be utilized in a separate system to generate steam at a higher pressure.
With reciprocating (piston) engines approximately 34% of the heat input is recovered as power, and 66% is unrecovered. All of the heat rejected to the jacket water is recoverable along with, depending on the engine, approximately 40%-60% of the heat rejected to the exhaust outflow. In some instances, albeit rare, aftercooler heat and lube oil can be recovered. For a gas turbine engine, approximately 29% of the heat input is used for power and 71% is lost due to exhaust. With a cogeneration system, 40%-60% of the exhaust is usually recoverable.
In a cogeneration configuration, there are two distinct cycles: topping cycle and bottoming cycle. In a topping cycle system electricity is the primary product and the residual waste heat is the primary mover. In other words, topping cycle plants produce electricity from a steam turbine with waste heat being the byproduct. During a bottoming cycle, the steam created first is used to provide power for industrial processes, such as a steam turbine, (primary product) with the lower pressure exhaust steam used to create electricity (primary mover). Bottoming cycle plants are less common throughout the world due to the high temperatures required.
Piston Engine Facilities
By far the most common method of cogeneration. The heat from smaller piston engines, usually diesel, is captured from the radiator or exhaust. These systems are popular because they are easy to maintain, cost less and are easily adaptable to a variety of size requirements.
Gas Engine Facilities
These plants utilize a gas engine which is generally easier to maintain than a smaller gas turbine (5 MW). The most common fuel used is natural gas or propane. These plants typically come as a complete package and are stored in a large warehouse type of room with connections to the heating, electrical and gas systems.
Gas Turbine Facilities
With these plants waste heat is generated in the flue gas of the turbine. The most common fuel is natural gas. Gas turbine plants typically are large and are not stored indoors but in sound attenuated enclosures with access to a gas line.
Steam Turbine Facilities
These facilities are fairly common and work on the principal of a heating system using the steam condenser to power the steam turbine.
Biofuel Facilities
These types of plants use a reciprocating gas or diesel engine depending on the configuration of the biofuel used. This design is quite similar to a gas engine plant. The primary advantage of a biofuel plant is the reduction of hydrocarbon fuel consumption and decreased carbon emission.
Historically, biofuel cogeneration plants have an easier time obtaining permitting than other cogeneration plants but are usually on the smaller side in terms of production output.
Heavy Fuel Oil Facilities
HFO plants are not widely used in cogeneration in the United States but are more common in developing countries. Fuel oil is the heaviest commercial fuel possibly made from the refinement of crude oil and is considered low-grade fuel.
HFO Number 5 and Number 6, which require preheating of 170 °F - 260 °F are the most common variants used in cogeneration plants. The benefit of HFO is that it is cheaply purchased but the downside is the emissions it produces are considerable.
Combined Cycle Facilities
Combined cycle plants work on the principle that the exhaust from one heat engine works off of the other to produce electricity or drive mechanical processes. The combination of multiple thermodynamic cycles results in increased efficiency and lowered fuel costs. The downside is that most cogeneration plants must be adapted to fit this technology.
Fuel Cell Facilities
Fuel cell technology works by converting potential chemical energy to electricity via a chemical reaction with an oxidizing element. Hydrogen is the preferred fuel to use however in cogeneration plants molten-carbonate or solid oxide are favored due to their high exhaust temperature, which can reach 1,200 °F.
Nuclear Power Facilities
Some nuclear power plants can be retrofitted with taps after the turbines to provide steam to a central heating system. These systems are not very common as the loss of electric power is about 10 MW to generate 95°C of heat.
Biomass Power Facilities
Gaining in popularity, biomass plants work by using hydrogen, carbon or oxygen from industrial waste or trash. In recent years, technological upgrades have been created to capture more output of energy from wood, garbage, waste products, alcohol fuels or landfill gases.
For the most part, there are a limited number of prepackaged cogeneration systems available for mid-sized to large scale use. The vast majority of systems are propriety designs built for custom projects. As always, it is best to consult a professional electrical contractor or design engineer before embarking on a cogeneration project. Professionals will be able to calculate the proper heat recovery for the prime mover to achieve the desired result.
Referenced: Bauer, Warner. 'Cogeneration Systems' p. 463-465 On-Site Power Generation 4th Edition. Boca Raton, Florida: Electrical Generating Systems Association, 2006.
>>Back to Articles & Info<<