Numerous food processing, packaging, and various packing plants utilize commercial and industrial power generators in their operations. One example
we have worked with and provided multiple generators sets to over the years is fish and seafood processing facilities. This article digs into the various
considerations food packaging companies have to take into account when considering a backup or prime power solution.
Seafood Processing Plants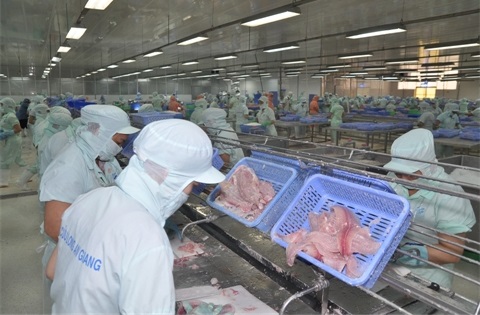
Seafood processing can be defined as the preparing of product for shipping to the final customer. In Alaska, fish, crab, and shrimp are commonly processed.
Many plants process multiple species of fish and crab. This allows plant production for more than one season. Quick processing of any seafood is critical. During peak season a worker will be on the line from 12 to 16 hours per day.
The work begins from the time the product is unloaded from the fishing vessel and ends when it is ready for delivery to the customer. Each facility can differ in product processed and the method of process. Larger plants use automated process equipment, while smaller plants complete the work by hand.
Backup Power
Some common electrically powered equipment used by processing plants are:
- Ice Makers - When fish are unloaded from the fishing vessel, they are packed on ice immediately
- Electric Cranes - Used for unloading crab and shrimp from vessel hold
- Conveyors - Transports product from one station to the next - the station can be an automated machine
- Automated Equipment - From automated fillet machines to machine that require operator interface (such as packing machines)
- Air Compressor - Automated equipment offer requires supply air to operate
- Water Pumps - Pressurize large cleaning systems so many workers can have clean water supply at the same time
- Flash Freezers - Freeze product quickly for packing
- Cookers - Used in canning process
- Freezers - Stores frozen product after processing and ready for shipping
- Coolers - Stores product to be delivered fresh
- Lighting - Plant and individual station illumination
Depending on size and operation of the plant, a power outage from a utility company can quickly result in lost product. Not all processing plants utilize all equipment listed above. Lighting, coolers and/or freezers and ice makers that do not have a power supply can cripple the bottom line of an operation. Installation of backup generator(s) can provide power during power outages from the utility company. Larger facilities use can use multiple generators connected in parallel.
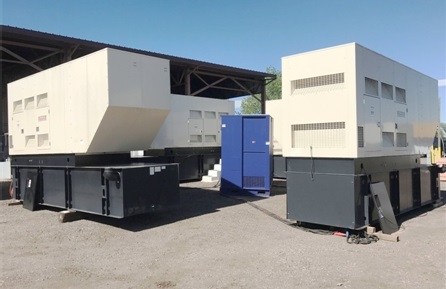
Prime and Continuous Power
Processing plants can be located in remote locations without electrical utility supply. While operating a processing plant in these locations offers challenges, the ease of receiving and shipping to a world-wide market can offset the challenges.
Dependable power challenges are answered with diesel generators. Prime power rated generators can serve processing plants that operate on a set schedule, such as eight hours per day, five days per week. Continuous generators can serve plants that operate 24 hours per day, seven days a week.
There are two methods for supplying power:
- One large generator - Supplies all electrical power, works but there is no redundancy in the system. If the generator fails, then the processing plant is completely without power.
- Multiple generators connected in parallel. When generators are connected in parallel the load capability is additive. Four 500 kW generators connected in parallel produce load capabilities of a 2000 kW generator.
- See the image to the right shows 4 500 kW generators connected in Parallel for one of our customers
Considerations
Always consult a professional through purchase, installation, setup and testing steps. When designing and purchasing a power generation system, consider:
- Sales - Help client through the decision of which generator and accessories best meets his needs. Test generator and arrange shipping if needed.
- Installation - Arrive at location and install the generator and. switching equipment for multiple generators used in paralleling applications. Removal of existing generator.
- Testing - Test operation of generator after installation. This includes placing generators on line in parallel and training personal.
- Troubleshooting - Qualified technicians are necessary when power generation equipment needs repairs/maintenance.
All generators must have a means to keep the engine starting batteries charged. If the generator is operating in a cold climate, it must have an engine block heater connected to a pow
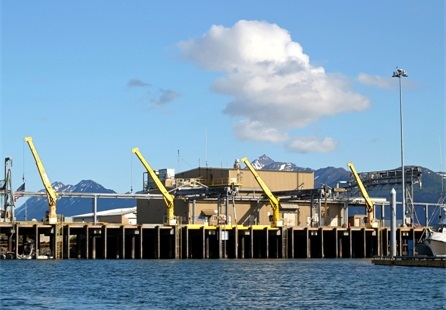
er source to insure ease of starting. All additional manufacturer cold weather operation precautions must be followed.
Many times installation, testing, maintenance and troubleshooting duties are shared by local vendors in a cost saving effort.
When installing a new power generator(s), it is good practice to one source purchasing, installation and testing. A fictional chain of events is listed below:
- Customer purchases multiple generators to be operated in parallel and verifies correct parallel operation on site at dealer.
- Location, pricing and other variables lead customer to using local vendors.
- Local vendor provides only certain services. Does not include complete demonstration of paralleling multiple generators. Contract does not include block heater or battery charger connection. Wiring contractor does not work with paralleling multiple generators and instructs maintenance to operate in manual mode.
- All generators are placed in manual mode. Maintenance starts first generator and closes feed circuit breaker. Second generator is started and feed is closed and trips immediately. Only one generator can be run at a time resulting in 500 kW instead of the 2000 kW desired.
- Facility has to adapt and shut down equipment to allow for 25% of supply power. Lack of battery charger and block heater connection result in failing batteries and hard to start units.
- Customer contacts supplier for troubleshooting installation and all issues are corrected for full capability operation.
Although the above example is fictional, technicians face this type of chain of events often. The best way to avoid preventable issues is to utilize companies that provide complete services, such as Generator Source. If not a possibility, review vendors capabilities prior to contracting them and include a statement of work containing all expectations is suggested.
>>Back to Articles & Info<<