The Kickoff of Automotive Production
Karl Benz is credited with the first produced automobile. He designed and built the first practical internal combustion engine powered automobile in 1885. The United States followed shortly afterward in the 1890s.
Henry Ford began building cars in 1896 and Ford Motor Company was introduced in 1903. The first Model T cars were introduced in 1908 and sold for $850.00. The introduction of the conveyor belt assembly line and mass production techniques reduced the price to $290.00 in 1927. Synchromesh manual transmissions, semi-automatic transmissions, automatic transmissions, hydraulic brakes, independent suspension and engines with overhead valve configurations were amongst the automotive technology break-through of the 1930s.
Auto production stopped in February 1942 when the United States entered World War II. Factories were converted to support the war effort by producing millions of tanks, trucks and other weapons. Additionally, aircraft factories produced tens of thousands of airplanes in the late 1940s and 1950s. The end of World War II triggered the factories to switch back to automotive production.
The only automotive companies to survive the Great Depression were General Motors, Ford Motor Company, Chrysler Corporation, Hudson Motor Car Company, Nash Kelvinator Corporation, Packard Motor Car Company, Studebaker Corporation. Crosley shut their doors in 1958. Packard and Studebaker merged but production ended in 1966. Hudson merged with Nash-Kelvinator and Formed American Motor Corporation (AMC) which was purchased by Chrysler in 1987. Independent automakers were competitors of General Motors, Ford, and Chrysler (the Big 3), and ended production by the 1960s.
Advancements in Automotive Manufacturing
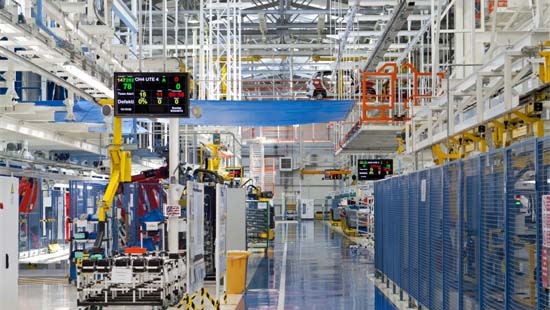
There are 14 Automotive Manufacturers in the U.S. with approximately 104 manufacturing facilities, excluding supporting facilities. Some examples of supporting facilities are:
- Specialty Engine Manufacturers - Such as Cummins supplying engines for Nissan and Chrysler Corporations
- Automotive Lighting - Headlights, interior lights and Light Emitting Diodes (LEDs)
- Engine Components - Belts, hoses, spark plugs, injectors, and other items
- Tires - All season, winter, mud and snow installed as options
- Bearings - Companies such as Timken, NSK and NTN supply wheel hub bearings
The above list is a small sampling of vendors that are used when a car is produced. Large trucking manufacturers (Mack Volvo, and Peterbilt), bus, Recreational Vehicle (RV) and motorcycle manufacturers are all part of the automotive world. Each has its own external vendors and suppliers.
Automotive manufacturing factories keep in step with the rapid changes in the technological world. Robotic arms weld bodies and automated material handling systems route the body to the next station. All have individual controlling software and connect together by electrical cables. Communication is shared throughout the body line. The body must complete the first stage in order to move to the next stage. If there is any interruption in the cycle, the system alerts the operator of the errors and stops the production run. Individuals do not perform the actual welding function but start the line and perform quality checks. Maintenance staff repair problems within the robotic arms and material handling systems.
There are many examples of automation in the production of automobile parts. Bearing manufacturers have turned to an automated process as well. The company receives forged inner and outer bearing races. Computer Numerical Control (CNC) machines that work on the popular X, Y, Z axis perform the initial machining process. Automated material handlers route the race to heat treat the machine. Heat treated races then move to the grinding process for final shaping. After the final shape is achieved, races move to super-finish process and a fine polish is placed on them. Inner races, outer races, ball bearings, and bearing retainers are assembled and passed to a grease machine. This machine adds grease and seals the assembled bearing. Bearings and hubs are assembled by a separate process. Each level of the process requires an operator that conducts quality checks.
Factory Auxiliary and Support Systems
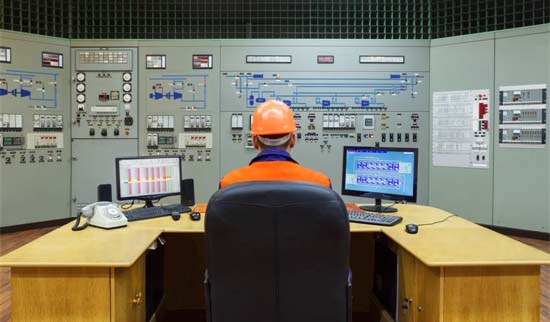
There is a fine line between auxiliary and support systems in the factory setting. Some maintain that an auxiliary system as one that directly supports production efforts. Emergency power, climate control, security and monitoring systems are among some of the factory supporting systems.
Auxiliary systems are defined by the production equipment they support. Most all factories require compressed air for production. Large air compressors require treated cooling water for intercoolers, aftercoolers and descant dryers. The cooling water tanks, circulation pumps, and cooling towers are all components that keep the air compressor at proper operating temperatures allowing plant air. Without compressed air, many factories have to operate at reduced capability or are completely shut-down.
Supporting systems contribute to operation by providing needed services to the plant. These services are not associated directly with automotive production, but the absence of the system can shut-down the production of the facility. Some factory floors require a temperature, humidity, pressure-controlled environment. This is controlled by a combination of Heating Ventilation and Air Conditioning (HVAC), ventilation fans, and humidity control systems.
When power is lost, emergency generators support the facility with power. They too have support systems. These systems operate both when the generator is shut-down and operating. Multiple generators running in parallel can route through machinery main control rooms. A combination of auxiliary control panels and software-controlled systems can be contained in one room. Each system features an individual alarm and monitoring system. Often operators man the control room to respond to alarms, cycle redundant equipment and monitor systems operating conditions. This allows for the quick response to maintenance issues.
Utility Power Failures
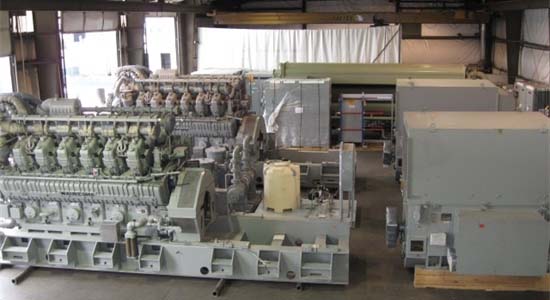
Manufacturing facilities consume a large amount of power. Many have dedicated sub-stations that provide high, low, and medium voltage supply. They can consist of distribution panels, circuit breakers and transformers. All equipment is subject to failure. Tornadoes, floods, hurricanes, ice storms, high winds, heavy thunderstorms and earthquakes often damage the equipment on the electrical grid. The time the power is out corresponds to the damage to the electrical grid.
Factories have emergency power requirements which are regulated by various Federal/State/Local agencies. The
National Fire and Protection Agency (NFPA) delivers installation requirements to satisfy human safety regulations. Each building on the factory complex can have emergency generator(s) for backup. These can be located indoors in a dedicated machinery room or outdoors in a sound attenuated enclosure.
If production is to continue during power failures, the back-up power system capabilities must be able to supply power at peak building electrical load, possibly for extended amounts of time. Generators and electrical distribution equipment must be maintained on a schedule determined by manufacturers and other regulating agencies. A properly designed, installed, and maintained system will provide power when the utility power fails.
We at Generator Source have been in the generator business for more than 35 years. Our pre-owned generator stock consists of generators of all styles and sizes. We also maintain new generator stock. All pre-owned generators must pass a 31-point inspection before placement on the ready yard. This allows us to often help arrange fir shipping within 24-hours of completion of the purchase. Go to
Inventory to view our generators. Our skilled staff can provide maintenance and troubleshooting including load testing.
Contact Us for any questions.
>>Back to Articles & Info<<