Diesel engine generator governors are sometimes referred to as the speed controller for the diesel engine. The diesel engine must maintain a pre-determined speed to maintain generator output specifications. If the engine speed is not correct the generator will not maintain the required output specifications.
This article will explore the different types of governors equipped on diesel generator sets.
Governors can be divided into two basic groups:
• Mechanical/Electrical Control – Older generator sets utilize these control systems. Fuel system is controlled by mechanical governor.
• Electronic Control – Newer generator sets use an electronic control system. This system interfaces and controls engine and generator control functions to provide a constant, reliable power source.
Mechanical/Electrical Control
Mechanical/Electrical Control systems were the first control systems introduced by generator manufacturers. This interfaced mechanical engine control functions with generator electrical load needs. Many generator control systems are available, all operate under the same design principles. A Woodward Control System is featured below:
• Woodward Governor – Engine speed is mechanically controlled by centrifugal governor. Governor receives analog input signals from controller.
• Speed Sensor – Magnetic sensor that supplies information to the Woodward controller.
• Woodward 2301A Controller – Receives signals from speed sensor and transmits signals to governor and external customer supplied switch boards.
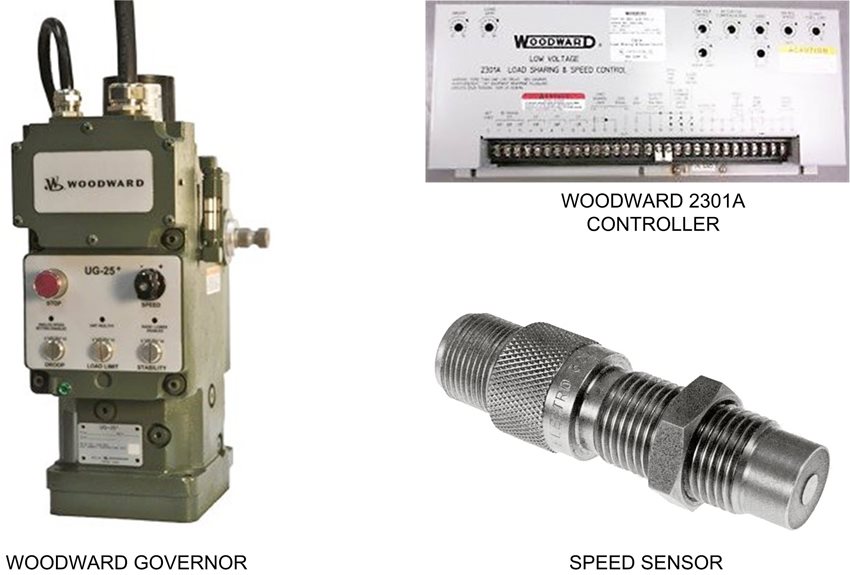
Figure 1, Woodward Control System
This control system is considered to be an analog control system. System settings are accomplished by with the use of adjusting screws turned in a specific direction to accomplish a required setting. Multiple generator control is offered with this system. Generator(s) supply power to a facility supplied switchboard control system.
Additional hardware installation can allow for remote communication and operation of the emergency power control system.
Electronic Control
Generator design and creation progressed with the advent of digital technology. To illustrate the interface between the engine, generator(s) interface control, this section is divided into the following areas:
• Analog and Digital Signal – Basic concept used when introducing a generator set that has an engine equipped with an engine ECM (Electronic Control Module), but does not have an internal control system.
• ECM – Define interface between ECM and engine functions for generator sets that are not equipped with advanced generator controls.
• Engine and Generator Interface Controls – Introduces integrated software package for engine and generator controls.
Analog and Digital Signal
It is important to understand the difference between analog and digital signals (Figure 2) when updating an older analog configuration to the newer digital control configuration:
• Analog Signal – Signal is defined as a sine wave. This signal is measurable and controllable through the complete cycle of high and low peaks. Specific adjusting screws allow individual system adjustments.
• Digital Signal – Signal is defined as a square wave. Inputs and Outputs from controller are in two states:
- OFF – 0 to 2.5 VDC
- ON – 2.6 to 5.0 VDC
If facility requirements dictate the need to interface analog signal(s) with digital signal(s). An inverter can be installed to change a digital signal to an analog signal. A converter can be installed to change an analog signal to a digital signal

Figure 2, Analog and Digital Signals
ECM
This example illustrates the interface between the components of a generator set that has advanced engine controls, but relies on external communications from and external control panel (Figure 3). The flow for example below was designed using information from a Cummins QSK45/60 Industrial Wiring Diagram. Component definition below:
• ECM – Receives input signals and transmits output signals to engine. Receives input signals from control panel.
• Engine – Generator prime mover. Receives input signals and transmits output signals to ECM.
• Control Panel – Receives input signals from generator and transmits output signals to ECM.
The engine ECM is the heart of the engine control. It has the ability to complete the information loop between the engine, generator and control panel. Digital and analog data transferred between the engine, ECM and Control Panel is either input or output. Below are some examples:
• Engine Transmit to ECM – Engine speed, temperature and coolant sensor. Fuel pump, timing rail and fuel rail pressure.
• ECM Transmit to Engine – Engine start, fuel shutoff, fuel and timing rail actuators and fan clutch.
• Generator Transmit to Control Panel – Generator supplies voltage to control panel for distribution.
• Control Panel Transmit to ECM – The control panel houses a customer supplied components.
Signals are transmitted to the ECM for throttle adjustments to maintain speed requirements.
Communication between the system components during a power failure for this system are:
1. Start signal sent from control panel (via automatic transfer switch) through ECM to engine.
2. Engine starts. ECM monitors engine functions and adjust fueling to accomplish preset engine speed. ECM can shut engine down during critical engine failures.
3. Generator sends voltage to control panel for distribution. Many control panels have ability to monitor generator operating statistics.
4. Primary power is restored. Control panel transmits engine stop signal to ECM. ECM transmits shutdown signal to engine.
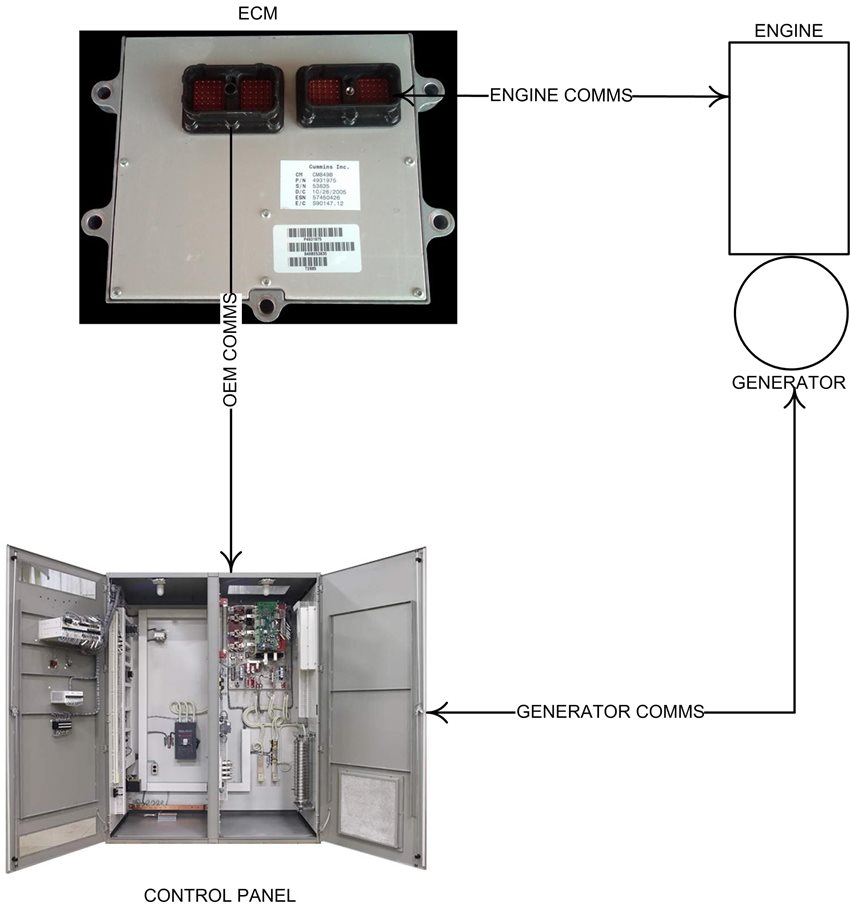
Figure 3, Advanced Engine without Generator Controls
Engine and Generator Interface Controls
Newer generator models were introduced with a full monitoring and control hardware and supporting software (Figure 4). Modules for paralleling capability were added. This arrangement could be in a redundant setup for critical emergency power supplies. If one generator failed, load is reduced and the other continues to support load.
In the below example two generators powered by Cummins QSK45 generators are used. The control system used is PCC 3200. The individual modules of the unit are used for:
• Fuel (Connector 02) – Communicates with input and output engine fuel system components.
• Base (Connectors 05 and 06) – Communicates input and output base engine function components.
• Generator (Connector 01) – Communicates input and output signals with generator.
• Parallel (Connector 04) – Allows paralleling of multiple generators.
• TB6 – Networking card. Allows network capability for each generator on the network.
The sequence of events during power failure are conducted under the basic concepts in the above mentioned ECM section. The differences are:
• All generator hardware and software contained in one operating system.
• Capable of paralleling multiple generators.
• Advanced monitoring and reporting capabilities.
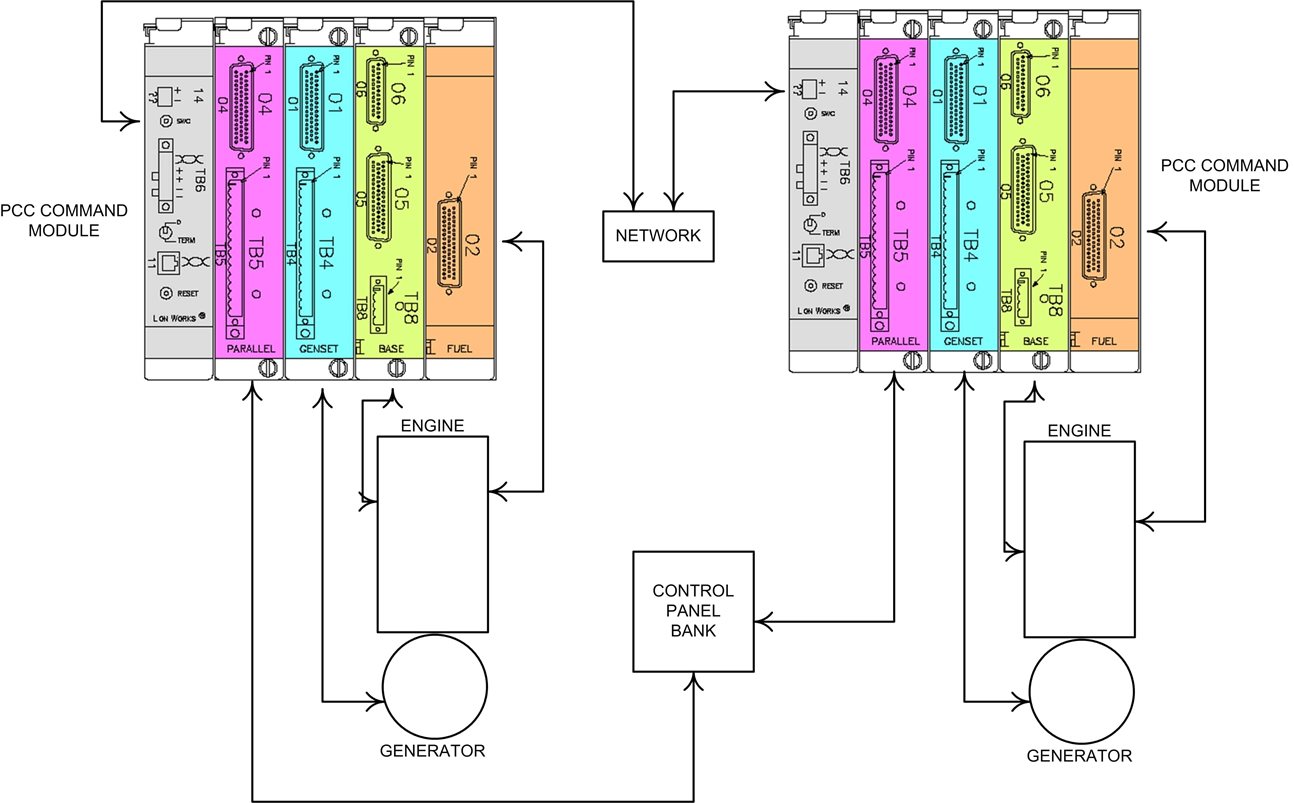
Figure 4, PCC 3200 Control ModuleFigure 4, PCC 3200 Control Module
>>Back to Articles & Info<<