Quarries produce needed aggregate, from crushed rock to sand, for the construction industry. Precious minerals such as gold and silver, along with a host of other valuable minerals, can be contained in hard rock. These minerals must be extracted from the hard rock by the use of a crusher.
Many quarries employ blasting as the first step to start the process. With this process, rock is broken so it can be retrieved from the area. Large construction equipment such as frontend loaders and backhoes separate the rock. Larger rocks that cannot be crushed are reduced to crusher acceptable size rocks and transported to the crushing site.
Rock Crushing Plants Produce Stone, Sand and Gravel
A rock crusher is a machine that reduces the size of a rock to smaller rocks, gravel, or sand. Rocks, sand, and gravel are classified into various sizes. Each crusher reduces rock to a predetermined size. There is more than one type of crusher available. Each style of crusher has an intended application as listed below:
- Jaw Crusher - One hardened jaw of the crusher is moved into the stationary jaw. Used in mining and quarries. Material can be dry to slightly wet.
- Cone Crusher - Includes compound cone, spring cone, hydraulic cone and gyratory crushers. A hardened cone compresses rock against a hardened surface. Used in sand and gravel production. Material can be dry to slightly wet.
- Shaft Impactors - Can be vertical or horizontal in design. These crushers use impact rather than pressure to crush the material. Used for sand, gravel and various materials.
Crushing rock produces large amounts of dust. It is not uncommon for rock crushers to contain a water system with nozzles to lightly spray the rocks prior to crushing. However, this does not completely reduce production of dust. Movement from a crusher with a larger rock classification to a crusher with a smaller classification, then to the finish pile always results in dust. Some rock crushers do not use any water and dust is produced at an extreme level.
Effects of Dust on Commercial Power Generators
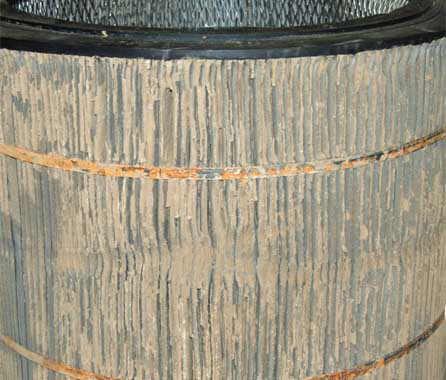
Large rock crushers require electrical power to operate. Power requirements range from:
- Electric power for crusher motor
- Electric power for conveyor motors
- Electric power for water supply system
- Electric power for lighting and control systems
Power does not pose an issue for crushing locations that have utility access, but it will in the event of a power failure. Many times, crushing plants are located in remote locations that facilitate easy access to quarry and outbound shipping.
For remote locations, the answer to the power supply questions is often the use commercial diesel generator. Generators in sound attenuated enclosures offer an all-in-one package. This includes the engine cooling system and fuel tanks.
The generator's diesel engine uses surrounding air for combustion. The air is routed through a filter contained in the attenuated enclosure. Original Equipment Manufacturer (OEM) filters are commonly single stage filters and not designed to operate in extreme dusty conditions.
When a filtering system is used in an environment that it was not designed for, a chain of failures with the filter begins. The filter media becomes clogged with dust and debris. Most diesel intake air systems are equipped with an indicator that shows red when the filter is beyond limits. If the engine is not shutdown, the filter will continue to accumulate dust and debris until the media fails. When the filter media fails, the result can be tears and holes. This allows dust and debris to enter the engine causing reduced life or complete engine failure. When the engine fails there is no primary power for remote locations or emergency power for sites with utility access.
Generator Upgrades for Customer Requirements
There are two types of filters basic styles of filtering systems used in diesel engine air intake systems. The two styles are:
- Single Stage Air Cleaner - Dust passes into the intake of the filter through the primary filter then into the engine. This is common filter for OEM applications.
- Two-Stage Air Cleaner - Dust passes into the pre-cleaner and filter to remove a large portion of the particulate matter. Once pre-cleaned the air is routed to the primary air filter and the remaining dust is filtered out. Two stage filters are used in heavy dust environments such as construction and mining industries.
Generator Source recently met with a client and identified solutions to the problems of operating in an extreme dusty condition created by crushing rocks for aggregate uses.
We started with a Cummins 750 kW generator in a sound attenuated enclosure. This provided a complete generation system to include fuel tanks, cooling, and control system. To overcome exhaust concerns, a pancake style muffler was specified. In order to install the needed muffler, the sound attenuated enclosure had to be removed and support framework fabricated and installed. Donaldson is a leading manufacturer of two-stage filters. We then installed a properly sized, two-stage filtering system for the conditions. The changes to the intake and exhaust system with proper maintenance allows for a long generator life in extreme operating conditions.
We can upgrade generating systems to suit a wide variety of applications that are often considered to be extreme. Let us know what your application is, and we can design a customized fit to accommodate your individual needs.